Nous leurs avions rendu visite il y a 3 ans (The secret of Lightweight wheels). Carbon-Sports, filiale de Carbo-Fibre Tec, a connu une progression fulgurante sur les derniers mois.
A l’origine, dans les années 90, les roues Lightweight, produit exclusif et exceptionnel que les pros et passionnés s’arrachaient, étaient fabriquées par Heinz Obermayer et Dierl Rudolf, dans un atelier rustique.En 2000, Erhard Wissler, investisseur et gérant de 7 entreprises d’envergure internationale reprit le flambeau.
Distribuées dans tous les pays où presque, Carbon-Sports s’est offert le luxe de devenir équipementier de l’équipe professionnelle Unibet, Canyon, puis Milram au travers d’une production décuplée et d’une marque qui s’impose de plus en plus comme LA référence.
Les roues Lightweight prirent une autre dimension.
Aujourd’hui, Carbo-fibre Tec représente quelques 150 employés. Erhard a investi dans un nouvel outil de production : une usine d’une superficie quatre fois plus grande que la première. Ses roues Lightweight représentent quasi la moitié de leur chiffre d’affaire annuel, quel bond en avant ! La seconde moitié du chiffre d’affaire est assurée par les autres secteurs d’activité : le médical avec l’arc scanner notamment, l’aéronautique avec Airbus, l’aérospatial et la course automobile avec des pièces que vous découvrirez plus bas.
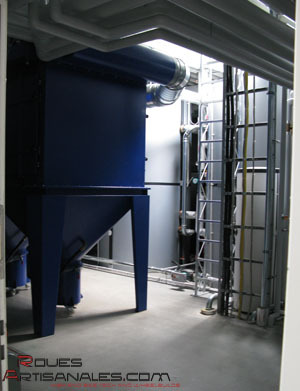
Récupération des gaz
L’usine implantée à deux pas du Messe – site gigantesque de l’Eurobike – présente tous les signes d’une réussite fulgurante et du modernisme qui l’accompagne. Ainsi, l’écologie a été placée au centre du développement de la nouvelle usine.
Pas de panneaux solaires, d’éolienne, de système de récupération des eaux usées comme on le voit souvent, mais un système de récupération des gaz brûlants issus de la cuisson des pièces carbone. Carbo Fibre-Tec a parfaitement adapté son bébé au profil de son activité et de ses particularités.
Le bâtiment complet est donc entièrement chauffé « gratuitement », ou en tout cas au travers d’un système de transformation des gaz que vous pouvez découvrir à droite.
L’économie est substantielle et correspond entièrement à la vague actuelle de l’écologie.
Signe avant coureur de la modernité, et surtout la technologie à laquelle nous devions nous attendre dans l’usine : la poignée de porte d’entrée est en carbone, de même que les escaliers pour monter dans les bureaux !

La touche qui fait la diffèrence!
Exposés dans le hall d’entrée très classe, les vélos d’Erhard affichent la technologie allemande et nous révèlent une surprise de taille: Carbon-Sports développe un système d’étriers de freins entièrement en carbone qui devrait voir le jour lors des prochains salons. La pièce est encore à l’état de prototype et sa forme sera modifiée. Vous pouvez cependant l’apercevoir sur le Pearl blanc ci-dessous. Nous ne publions pour l’instant pas de gros plans de cette pièce pour des raisons évidentes de discretion souhaitée par le constructeur.
La fabrication des pièces carbone demande une main d’oeuvre très qualifiée. Les pièces chez Carbo-Fibre Tec ont une âme en mouse habillée de fibres de carbone pré-imprégnées. Ceci permet une résistance et une rigidité importante tout en conservant un poids assez faible. Les fibres de carbone sont conservées dans un congélateur afin de préserver leurs qualités.
Après « l’habillage » des âmes, les pièces sont placées dans leurs moules sous une pression extrême et enfournées à des températures élevées pendant plusieurs heures. Les fours de différentes tailles et particularités se trouvent dans plusieurs section du site.
La section « fabrication des roues » est celle qui nous aura la plus impressionnée. Nous appellerons cette partie, la « zone 51 » de l’usine Lightweight! La concurrence européenne, américaine, et surtout asiatique se serait trop réjouie de photos de la fabrication, évidemment non autorisées.
Faute de photos, nous pouvons tout de même décrire brièvement la fabrication d’une roue.
Grosso modo, les fibres de carbone d’un côté de la jante sont posées sur un moule, les rayons sont enroulés autour du moyeu et tendus avec une force extrême via des molettes. Cette procédure est éxecutée une seconde fois, pour l’autre côté de la roue. La structure en mousse est placée entre les deux parties, puis l’ensemble est passé au four. La jante est sous haute pression dans son moule, il en ressort quelques heures plus tard le produit fini, ou presque. Ne manque plus que quelques finitions: peinture, ponçage, réglage du voile.
En ce qui concerne la version pneu, la production est complétement diffèrente puisqu’a priori la roue est fabriquée en 2 parties distinctes, fabriquées avec force pour assurer la résistance à la pression et à l’impact.
Le réglage du voile ou les répérations sont effectuées dans une pièce diffèrente. A la sortie du moule, les roues sont normalement parfaitement droites. Quand elles ne le sont pas, elles peuvent être dévoilées sur un banc spécial.
Pour les « dévoilages » post-fabrication, la jante est chauffée puis redressée sur les bancs spécifiques.
L’équipe Lightweight effectue aussi divers tests sur le suivi qualité des produits ou sur le développement des futurs produits.
Lightweight teste toujours de nouvelles fabrications. Après plusieurs années, la version pneu des roues mythiques est enfin disponible en très petites quantités. Le dérailleur l’est aussi dans des quantités tout aussi petites et un tarif tout aussi élevé. Le système de freins verra le jour, nous l’espérons l’an prochain.
En bref, sur la base des trente-cinq heures de travail de la législation française, l’achat d’une paire de Lightweight représente près d’une semaine de travail pour une personne! 28 heures pour être précis.
Une nouvelle technologie semble voir le jour puisque dans la salle de réunion « traînait » une roue avant à 6 rayons seulement. A priori, les rayons ne sont donc plus doublés, de jante à
jante, mais indépendants les uns des autres… Une astuce issue d’une technologie spécifique qui devrait résulter en de nouveaux produits dans quelques temps…