
Despite rapid breakthroughs in composite materials, we have to realise that not even the major manufacturers have been able to make a light, strong, reliable full carbon clincher rim. A set
of very demanding parameters make clincher rims some of the most difficult components to design and manufacture from carbon: holding air pressure, high impact resistance, resin resistant to
high temperatures from braking, low heat transfer properties of the carbon fibres.
That’s why the carbon clincher wheels have never been a good deal because of their lack of reliability and resistance.
A system that meets some extreme requirements
Because of the clincher rims’ « hook » architecture, composite fibres are far from being the most appropriate material: they lack resistance to the forces created by the bead of clincher
tyres. Behind the visual simplicity of a clincher rim, extreme strains are exerted by the pressure of the tube: the hooks need to resist up 3.5 tons at 10 bars (145psi). An alloy rim has
excellent mechanical properties for this task. However alloy rims are heavier than carbon rims, meaning higher inertia and lower performance.
At this point things are getting complicated: designing a carbon tubular rim is straightforward, but doing the same for a clincher rim is a different story. First the carbon is about 10
times less compression resistant, while taking into account the resin and the off-axis fibres, than a good alloy. Second, the resin heats up a lot with sustained braking and tends to
distort.
Paul Lew tried to overcome these challenges and the solution he has chosen is brand new in the bicycle industry. Instead of reproducing exactly the hook system of the alloy rims,
which was a result of early wire bead clinchers which needed a hook to prevent them from stretching, he went to a complete different solution, which is much easier to manufacture and allows
ultra resistant and light components.

BSC: a subtlety with a big impact…
The hook system disappears with BSC technology (« Bead Seat Clincher« ). This is so obvious that no manufacturer thought about it… As mentioned above, the
hook system was not modified since the first clinchers with wire beads. These beads could stretch with the inner tube air pressure, so they required a hook.
Nowadays, high end clinchers are all equipped with kevlar beads to make them lighter, but this lightness comes too with an amazing resistance to stretching. Moreover their length of life
is, like many composites, exceptional. Thus, the tire can stay perfectly in place in spite of the high pressure.
This important modification, combined with the materials and a special resin, give several advantages. The most important is certainly the position of the bead: it concentrates the forces
generated by the inner tube pressure to the bottom of the rim chamber instead of the hook system that concentrates the strains on the sides. Beside of this, the rim specifications are
attractive:
1 ) The brake track thickness is three times higher than for a standard hook system:
* clincher pressure resistance, no pressure limit, except that of the clincher itself
* impact resistance three times higher (to equivalent composite materials, the boron/carbon structure being already more resistant than a carbon/epoxy
structure)
* higher lateral stiffness
2 ) Hybrid composite, the carbon fibre is boron reinforced, like the complete wheels or the tubular rims. The mechanical properties exceeds that of either fibre alone:
* impact resistance, the rims are so resistant that one will be able to use them for cross
* resistance to flex
* stiffness
3 ) Resin resistant to temperatures over 200°C (400°F):
* the rim does not distort, even after sustained braking
4 ) The molding is easier than the hook system rims that requires a post molding step
5 ) Pinch flats are greatly reduced
6) Better placement of the beads:
* much more favorable tire shape
* smoothness and fluidity on the road
|
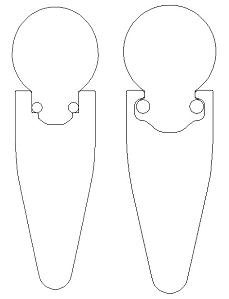
Left: cross section of a Lew Pro VC-1
Right: cross section of a hook style rim
|
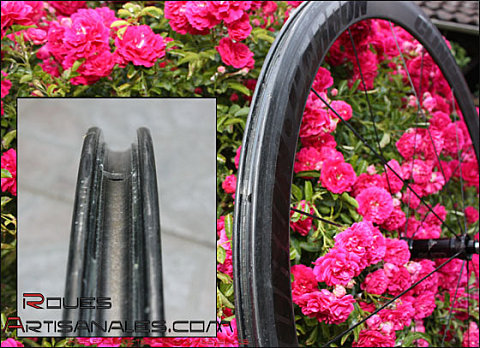
Thus, to make a clincher carbon rim, manufacturers like Zipp have to use an alloy rim with a carbon fairing, which is strong but heavy too. Some others, such as Corima make them entirely
out of carbon but limit the clincher pressure to 8,5 bars, or Reynolds (old Lew process) at 10 bars.
The Lew Pro VC-1 has the advantages of both without the disadvantages.
Table comparing the clincher rims of similar depth:
Model
|
Height
|
Weight
|
Max. pressure
|
Architecture
|
Lew Pro VC-1
|
46mm
|
380g
|
clincher pressure
|
full carbon
|
Zipp 417 (303 wheels)
|
44mm
|
560g
|
clincher pressure
|
alloy rim/ carbon fairing
|
Corima Aéro HP
|
45mm
|
490g
|
8,5 bars
|
full carbon
|
Reynolds DV46C
|
46mm
|
460g
|
10 bars
|
full carbon
|

Kevlar beaded tires
The Lew Pro VC-1 accepts any clincher as long as they have a kevlar bead. Any medium to high range clincher uses this kind of bead, so no worries on this point. The only clinchers still
using mettallic wire beads are very cheap, heavy and are not really on a par with the performances of the rim itself.
The first impression we had when we saw this system was that the clincher would be unseated at high pressure. Paul Lew reassured us: « the pressure pushes the bead against its
seat because it is uniformly distributed. If you look a at wheel from the side, the pressure at the valve pushes the clincher to the exterior, which pushes the bead against the rim on the
opposite side. It happens on the whole rim so the tire can’t leave the rim unless it completely losses its annular structure«
So although the first inflation was done with some trepidation our fears proved unfounded.
We have a first ride at 9 bars.
On the road, we could corner at high speeds without any impact on steering. The first wheel was equipped with a Continental Grand Prix 4000s offering a very low rolling resistance and
definitely a good cornering grip.
Lew Racing advise not to exceed the manufacturer maximum clincher pressure, for obvious safety reasons. Moreover, if you plan long descents with sustained braking, it is recommended you
keep one to two bars below the tire’s maximum pressure because the rim will heat up and the inner tube will get pressure.
Lew Racing 2009 logos
Finally, the rims have new but still understated decals. They are bigger, nicer and easier to read.
The clincher rim obviously receives a special « Clincher » decal.
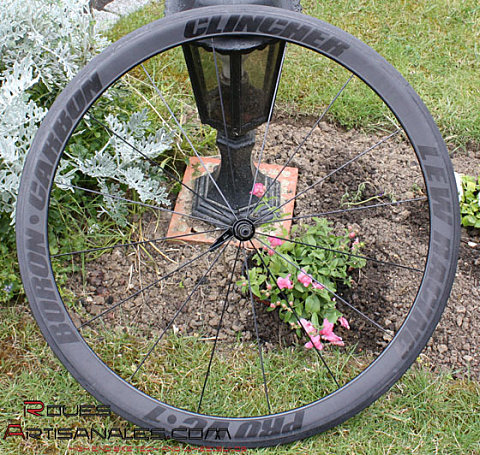
The price will be on par with the B+ (sub 250g) tubular rim which is US$1200 or about 800 euros.
More information on this page: Lew Clincher
|